When I was growing up in the early 1980s, one of my favorite games for Atari was Pitfall. If you recall, the goal was to maneuver “Pitfall Harry” through a jungle of hazards, one of which was swinging on a vine across a pond with three alligators.
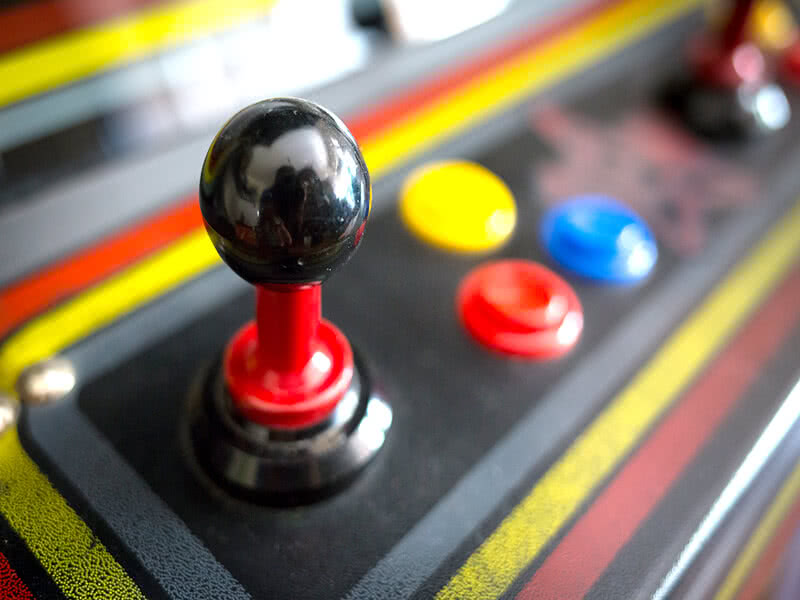
It was direct and simple. You had three lives to complete the game, and if the alligator got you, that round was over. Today, I try to save data centers from pitfalls that are common in cooling system execution. One of the biggest is when someone decides to replace integrated thermal unit controls with third-party controls.
Customers use third-party controls primarily because, for much of the past, factory-packaged controls that came installed on cooling units could not be easily programmed to accommodate the customer’s desired cooling operating sequences or routines. Fortunately, today’s advanced thermal control systems, such as the Liebert® iCOM™ thermal controls that are integrated into our data center cooling units, are programmed with multiple sequences of operation that can be selected based on the application to provide a highly flexible solution and greater controls capabilities.
There are four “alligators” to consider when using third-party controls for thermal cooling units:
Alligator 1: Improper Programming
Alligator 2: Building Management System (BMS) Integration
Alligator 3: Lifecycle Sustainability
Alligator 4: Costly Installation
Alligator 1: Improper Programming
Controls do only what they are “told” to do, so if you take responsibility for programming set points, sensitivities and other unit operating parameters, be aware that these changes may come with risks. The last thing you want to do is program problems into your thermal system.
Poorly tuned controls put operating routines, thresholds and failure scenarios at risk, leading to downtime, inefficient operation and excess component wear and tear. Now, fine-tuning integrated controls for optimal protection and efficiency can be tricky. But it becomes especially challenging with third-party systems. Errors in programming can potentially reduce system protection and efficiency, sometimes at great cost.
I recently visited a customer who replaced their factory-integrated cooling unit controls with a third-party system, so they could more easily manage remote unit operations. Unlike with integrated controls, the customer’s third-party controls did not come pre-programmed with prescribed unit failure scenarios and these had to be programmed into the controls. The result was a small disaster.
As the unit went into a low pressure condition, the new controls failed to respond with a capacity change to avoid unit downtime. This resulted in a coil freeze condition, which shut down the unit anyway, at substantial cost to the customer.
In contrast, integrated controls come with operating parameters and routines set for each unit. In the case above, they would have engaged self-healing routines as the unit approached the abnormal operating condition and reduced capacity to extend runtime and then notifying the user, thus preventing downtime.
Additionally, excessive wear and tear on components is also a risk when controls are not properly mapped to unit routines. For instance, in chilled water systems, poorly tuned controls can lead to unwanted conditions, such as wider fluctuations in temperature and humidity than is desired, and to frequent oscillations in water valves, all of which reduce equipment life and waste energy.
Another example of risk would be trying to program return air temperatures higher than a certain type of refrigerant and compressor would allow. While running return air temperatures at 95oF might work well for a unit using R410 refrigerant, setting controls to allow that same temperature in a unit running R407c refrigerant will likely result in unit failure.
Alligator 2: BMS Integration
Some data centers put their BMS in charge of cooling units. Data center managers may do this for a number of reasons, such as wanting to maintain a specific proprietary control strategy, wanting a standard user interface across different makes of cooling units or wanting functionality provided by the BMS that isn’t available in the existing unit controls.
However, integrating third-party control operations into Building Management Systems (BMS) requires a lot of on-site testing and unnecessary cost – an inconvenience if you’re trying to meet strict start-up deadlines and budgets.
Since data centers often have multiple types of cooling units, each unit requires different programming to the BMS, resulting in a lack of consistency in how the units communicate. Trying to scale such a system is difficult because of the additional hard-coding required. Getting it right requires a significant amount of engineering time and effort.
I have also seen situations where the BMS becomes a communications bottleneck. Delays in monitoring unit-level inputs, such as temperature sensor data, can delay unit response times. In one such case, this bottleneck created a lag in moving into and out of standby mode, resulting in ongoing hot spots.
In contrast, our integrated Liebert iCOM controls eliminate reliance on a BMS to control cooling units and the programming challenges. That cuts deployment costs by up to 80 percent, compared to using a BMS. Our Liebert iCOM controls can integrate faster and more easily to a BMS through pre-defined interfaces and mapping. They provide insight into cooling unit and thermal system operation while still maintaining unit control for redundancy.
Alligator 3: Lifecycle Sustainability
Commissioning unit controls is all about optimizing them for conditions that exist at installation. After commissioning, how will you ensure your data center thermal systems will operate as defined through varying operational states, such as low-load conditions and fluctuating outdoor temperatures?
There are many service companies with controls experience, but relatively few have personnel with specific experience in data center thermal controls. This makes continuation of maintenance and ongoing tuning a greater challenge. We sometimes find that original programming steps and subsequent component upgrades are not consistently documented, leading to future mistakes and mishaps. To ensure rapid response in the event of problems, some companies go as far as to keep a controls vendor technician on site.
Or course, this is costly.
Liebert iCOM controls support lifecycle sustainability by providing digital maintenance logs, troubleshooting instructions and automated routines that simplify programming and maintenance.
Every system activity and change is documented and quickly available. A network of local service experts ensures rapid response without the need to keep a third-party technician on site.
Alligator 4: Costly Installation
Programming third-party controls for specific unit operations, multi-unit routines and BMS integration is not easy. It can take months to complete such an installation, at a very high cost.
In contrast, integrated controls can be installed across the data center in just days. They come ready to operate with relatively few changes, because they are programmed for their specific units.
Configuration files can be used between units to maintain consistency in settings, reducing installation times. New configurations and floor layouts can be added in minutes. Auto sensor detection and configuration cuts sensor deployment times in half. Unit retrofits can be done in less than an hour. Today’s integrated controls provide companies with the benefits of easier, lower cost installation, plus the advantages of greater configuration flexibility.
Avoid the Alligators
While integrated controls once lacked functionality desired by some data center managers, today’s integrated controls now have superior features, such as advanced machine-to-machine communications, teamwork, powerful analytics and self-healing routines. Their programming routines are much more flexible and can be performed much faster and at lower cost than previous generations.
We’ve spent decades innovating our controls to operate data center cooling systems without a hitch. If you’re planning to implement thermal controls, doing it on your own with third-party systems might at first seem like the best route to your destination. However, weigh the benefits of today’s new advanced, integrated controls, before you swing over that pond of alligators.